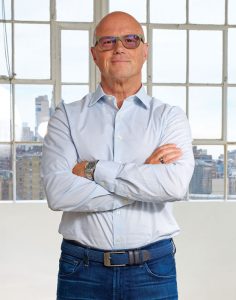
Reju™CEO Patrik Frisk spoke with Textile World about the company’s new Regeneration Hub Zero and the drive to make meaningful progress towards circular polyester.
TW Special Report
Circularity in textiles — reusing materials instead of turning them into waste — is possible and getting closer. Innovative companies are developing methods to recycle various types of textile waste, keeping clothing out of the landfill and reducing the reliance on virgin polymers.
Reju™ is a new company entering the circular conversation. This Paris-based start-up intends to offer a circular recycled polyester (rPET) chip that can be recycled an infinite number of times. Reju also is expected to have a 50-percent lower carbon footprint than virgin polyester confirmed via a life cycle assessment conducted by Deloitte.
“What has been holding the world back in textile circularity is not a lack of demand for textile recycling, but the lack of a solution that makes recycling of textiles economical onan industrial scale,”said Arnaud Pieton, CEO of Technip Energies, the France-based parent company of Reju.
Reju, led by CEO Patrik Frisk and COO Alan Poincheval, is capitalizing on a glycolysis polyester recycling technology named VolCat that was originally co-developed in a collaborative venture among partners IBM, Under Armour and Technip Energies, although Under Armour is no longer involved.
Reju broke ground on its demonstration plant located in Frankfurt, Germany, in the fall of 2023. The facility, known as Regeneration Hub Zero, recently opened, and it is expected to begin delivering polyester chip in 2025. There also are plans for additional hubs in the United States and Europe.
“We’re starting with the most urgent problem in textile waste — polyester,” Frisk said in a press release about the launch of Reju. “The world produces 92 million tons of textile waste each year, yet less than 1 percent is recycled. It is a system that extracts finite resources creating textile waste with no responsibility for end-of-life. Reju is going to change that by unlocking a new system through critical partner-ships around the world. We will build infrastructure, scale technology, comply with regulation and, in the end, help the textile industry evolve and enable a change in behavior. Our Regeneration Hub Zero in Frankfurt is a significant milestone, showcasing how this advanced technology addresses the global textile waste problem.”
Textile World recently had the opportunity to speak with Reju CEO Frisk to learn more about the company. Frisk is a Swedish-American textile industry veteran who began his career in the industry with W.L. Gore & Associates as a fabric salesman. His career path took him through the doors of storied companies and brands including VF Corp., The North Face, Timberland, Aldo and Under Armour in the United States as well as in Europe. Frisk first became involved with VolCat during his time at Under Armour, so it was a natural progression for him to take the job as CEO of Reju.
TW: What’s the biggest misconception about polyester fiber and apparel that you would like to address?
Frisk: One question often asked is why don’t we just stop using polyester and switch to more natural materials or something else? Unfortunately, that’s currently not possible. Polyester is a useful material for the textile industry, carpet industry, automotive and airline industries, bedding, packaging, and others. We can’t live without it for the foreseeable future. At the same time, polyester is the biggest contributor to global textile waste — only 15 percent of the polyester we make is even recycled, So, we need to understand how to live with it in a much smarter way, which is why we’re breaking it down and regenerating it. We’re finding new ways to use the resources we have.
TW: How does IBM’s VolCat technology play a pivotal role in Reju? How does the company’s process differ from that of other companies working to recycle polyester?
Frisk: Reju’s proprietary technology, which originated with IBM research, is the key to unlocking the circular textile system we are building. Reju is developing the infrastructure to take textile waste and regenerate it at scale, starting with polyester. The technology is the key to making this a reality.
Our work is focused on solving one of the largest societal problems of the future which is textile waste. Our approach and technology are different in that we are able to handle and are focused on mixed post-consumer waste and the extraction of polyester from this waste, something our technology is uniquely able to do.
TW: What are the biggest challenges facing Reju as the company scales up its recycling efforts, and how is Reju preparing to address any challenges?
Frisk: Our biggest challenge is that the new system to enable circularity does not exist, so we need to help build this out while we continue to build our own part of this new economy and system.
We have been working to identify how the entire new system and its infrastructure needs to come together to ensure a steady feed stream for our regeneration hubs. It requires specialized knowledge in waste management and reverse logistics in combination with an under-standing of textile fiber composition and chemistry. At Reju, this is part of our unique approach and talent of our organization.
TW: How does Reju contribute to the circular economy, and what steps are being taken to close the loop on polyester recycling?
Frisk: Reju is working to close the loop between upstream feedstock partners and downstream brand offtake partners by regenerating the collected materials. The industry has been on a linear model for decades and it will take a lot of work to make it circular, but we are optimistic that it can be done.
TW: Reju is promoting an open supply chain with 100-percent traceability. What technologies will be employed to ensure the process is traceable?
Frisk: We are working with our partner IBM to create a traceability platform that will support our Reju guarantee of textile-to-textile regenerated polyester, where we never lose chain of custody from textile waste to regenerated polyester.
TW: What are your main priorities for the company in the coming year? How do you see the role of advanced technology such as Reju’s in transforming the polyester apparel recycling industry over the next 10 years?
Frisk: We recently announced the opening of our first operating unit — Regeneration Hub Zero — in Frankfurt, Germany. This is Reju’s first major mile-stone after being incorporated just 12 months ago in Paris, France. The Hub was built in record time and is expected to begin deliveries in 2025. We have plans to build more Regeneration Hubs in other markets, including in the United States. It’s going to take the entire polyester ecosystem working together to solve the problems created. And we know this is going to take time to build the circular system — we’re talking about a generational change — but it doesn’t mean we shouldn’t start.
TW: How important is collaboration between recycling technology providers and the collective textile industry in order to have the biggest global impact?
Frisk: The massive size and global nature of the problem we’re trying to solve makes it impossible for any single organization to make meaningful progress on its own. Our goal is to create an industry where textiles aren’t wasted, but recirculated. Partnerships are critical to ensuring we can accomplish this at scale and that we can drive global awareness and adoption.
TW: What excites you the most about the work being done at Reju?
Frisk: At Reju, we have a wide variety of expertise, but there’s one thing we have in common — we’re all radical pragmatists. We’re staying grounded in reality, dealing in facts and the truth — even when it’s hard to swallow — and we’re working across engineering, technology, and textiles to solve one of the hardest problems of our time.
Editor’s Note: Since TW‘s interview with Frisk, Reju has announced plans for a multi-year initiative with Goodwill® and WM® to advance textile recycling in North America.The plan includes a collaborative model for regional textile collection, sorting, reuse and recycling with the goal of diverting nonwearable textiles from the waste stream.
2024 Quarterly Issue IV